As more attention is turned toward autonomous field operations, even companies that haven’t been known primarily for offering powered systems are revealing their efforts to produce self-propelled robotic equipment. Recently, tillage equipment producer Lemken announced it had partnered with forage-focused Krone (both companies are based in Germany) to create an autonomous power unit capable of doing a variety of tasks, using implements built by both companies.
While Krone has experience with self-propelled forage harvesters, powered equipment hasn’t been something Lemken is known for on this continent.
[VIDEO] AgDealerTV: Combined Powers
Read Also

Case IH, New Holland dealers to see more integration
CNH plans for “more than 15 new tractor launches, 10 combine launches, 19 crop production launches and over 30 precision technology releases between now and the end of 2027.”
Their Combined Powers project has resulted in the development of a fully autonomous power unit designed to work with Lemken tillage implements and Krone haying attachments on a three-point linkage. In all, the power units have three possible attachment points, rear and front linkage and a top connection point. The companies say the concept power units have been in field trials for a year, working in a variety of field conditions — and those trials are continuing. The goals being pursued by the project team are to eliminate the need for a conventional tractor and providing an autonomous machine that can do field work even better than a human operator can.
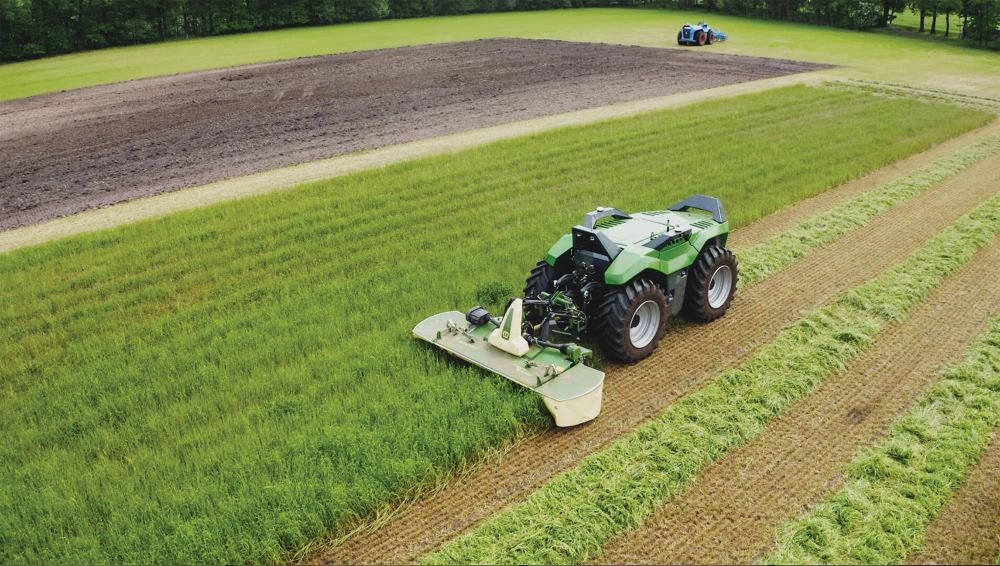
Focus on field work quality
Rather than just focusing on a power unit capable of accurate guidance across a field, the unit is designed with a primary focus on the quality of the field work it does, the companies say. The power unit is able to do that through complicated software that relies on AI (artificial intelligence). It uses a variety of sensors to gather data and interpret its surroundings.
“The speciality of the process unit is it is controlled by the implement and not vice versa,” says the description in the press release. “This detail was considered imperative for achieving optimum results. The implement and the drive unit act as one integrated smart system. Based on the long experience in the application of ISOBUS and TIM on Krone and Lemken machines, the drive unit and implement communicate and interact, sharing literally all types of data.”
The autonomous units are built around a 230-horsepower diesel engine, but power is transferred to the drive wheels and PTO via an electric drive system rather than a conventional mechanical powertrain. The companies say they chose an electric driveline because the industry is entering a “post-combustion engine era.” Using this approach will allow for an easy replacement of the diesel engine as a power source in the future with such systems as battery-electric or hydrogen power.

Three steering modes
The unit is capable of both pulling and pushing implements, and it’s compact — only 5.5 metres long and 2.7 metres wide. Three steering modes, front-wheel, rear-wheel and four-wheel steering, make the unit very manoeuvrable. It rides on four, 38-inch drive tires for maximum traction.
The intention is to have the machine’s progress monitored remotely through a mobile device, allowing it to provide progress reporting to the operator. At the moment, a radio controller is used to control the power unit for connecting to implements, but that function will eventually be enabled through a mobile device as well.
“Operators control and monitor the combination from a mobile device, transmitting jobs and job reports via a communication module and the agrirouter, the established data exchange hub,” the companies explain.
The Combined Power project is also aiming for a high level of reliability, with the intention of having the units capable of operating 24 hours a day.
As development and field trials continue, the companies are inviting comments from potential buyers about what functions they would like to use the units for through a survey feature on the website www.combined-powers.com.
“Thanks to its enormous versatility, the unit is designed for year-round work and a long service life,” said the companies this spring. “Intensive trialling in all types of conditions and seeking feedback from farmers and contractors will continue this year.”