As concerns over chemical usage and weed resistance increase, different technologies have been offered as alternatives to weed control. Recently, two U.K.-based companies have teamed up to produce a system that uses electricity to kill weeds.
“The principle of electric weeding has been around since the late 1800s,” says Jonathan Henry, managing director at Garford Farm Machinery. “So as an operating principle, it’s not a new one.
“The way it works is by passing current through the plant. It heats the fluid in the plant cells, vaporizes them and that damages the plant cells. Basically, after that happens the plant dries out, desiccates and dies.”
Read Also

Case IH, New Holland dealers to see more integration
CNH plans for “more than 15 new tractor launches, 10 combine launches, 19 crop production launches and over 30 precision technology releases between now and the end of 2027.”
Garford, which has been building row-crop tillage equipment, has partnered with RootWave, which developed the electrical technology. Together, they’re introducing the “eWeeding” technology to the market, starting in the U.K., with plans to expand it to North America. It will eventually be marketed here through Garford’s existing dealer network.
So far, Henry says, the company has had a lot of interest from organic growers, because this system offers a very high efficacy rate. One that is comparable to chemicals.
“That’s one of the things about electric is it’s an alternative, organic-approved non-chemical solution, and it has that enhanced efficacy by being able to treat the root. In the end we’re using physics rather than chemistry.”
READ MORE: Slow burn: Weed control at 0.2 kilometres per hour
A PTO-driven generator creates high-frequency AC power, fed down to a series of electrode pairs, one following the other. As one electrode contacts a weed, the high voltage passes through it and follows a return path through the soil to the following electrode.
“What we do is apply two electrodes to the ground,” he adds. “The electricity passes from one to the other through the soil. If you have the second electrode following the first, you actually get a second dose, basically. You treat it the first time you pass and you treat it again the second time.
“If you use the soil as the return conductor you can destroy the root as well, and thereby achieve a systemic treatment. Aside from chemicals, which are systemic, most other weed treatment agents are not. They treat the foliage above the ground but not the root.”
Any plants that don’t come into contact with the electrodes are not harmed by the electricity. Neither are any of the beneficial organic elements in the soil.
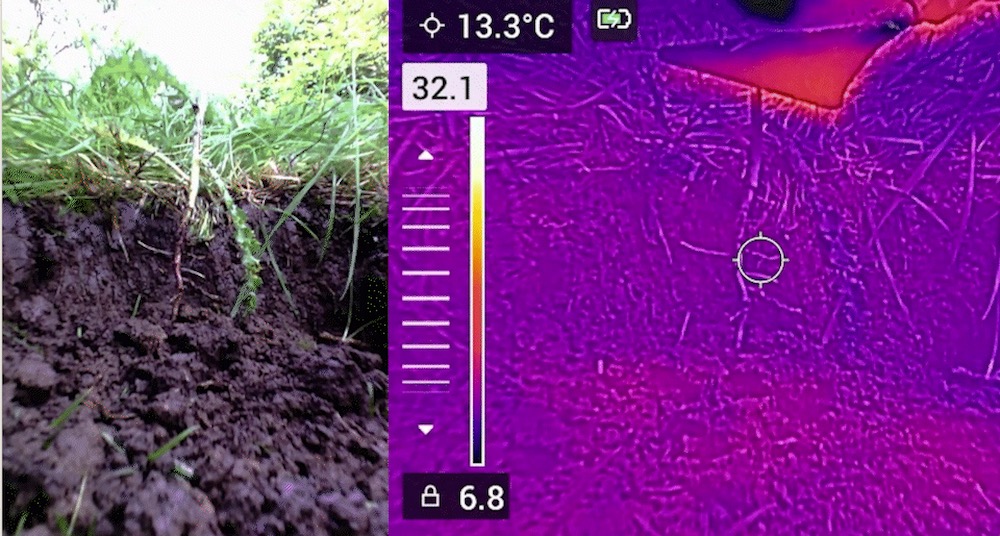
“One of the questions that often comes up from customers, does it have a negative impact on the biology of the soil?” he says. “Rootwave and others have done quite a bit of work in that space and none of those studies have detected any negative impact on the other soil biology, micro fauna, nematodes, fungi, bacteria, et cetera.
“There are multiple paths for the electricity to return; it’s such a large mass, therefore there is no significant heating in the soil structure. So it does what you want. It kills the weed and doesn’t hurt anything else.”
READ MORE: A shocking way to terminate plants without herbicide interventions
Using high-frequency AC power also reduces the risk to anyone that might accidentally come into contact with one of the electrodes.
“We’re using 18 kilohertz AC,” he explains. “The reason for doing that is it makes the high-voltage electricity safer in the event there is inadvertent human contact. The principles behind that are at very high frequencies electricity passes through the skin rather than through the internal organs.
“You don’t want to be touching it, because it will still burn you at these power levels, but it won’t create a cardiac event in the way DC or lower-frequency AC would.”
Producers interested in the system would need to contact the company to discuss how an eWeeding system could be configured to meet their needs, because there are a number of variables to consider.
“When we specify a machine for a customer, we need to have a detailed discussion with him about their production system,” Henry says. “A key piece is ‘What growth stage are those weeds going to be at when you want to kill them?’ because the amount of energy needed varies proportionally to the amount of biomass and the amount of water in the plant.
“The more water there is the more energy it takes to heat it up. When they’re small it doesn’t need very much, but when it’s larger you need a lot of energy.
“That determines how wide the machine can be. When weeds are at an early growth stage, which is what we think most producers will want, then we’ll be able to build wider machines for higher productivity.”
Initially the company will offer 60-kilowatt versions. But there are plans to develop 90-, 120- and 180-kW models that will allow for wider toolbars. The software in use on the current model controls the amount of power output from the generator.
However, the company is also working on more advanced software capable of looking ahead of the implement to estimate the amount of biomass, which will determine how much electricity is needed to do the job, rather than put out full power all the time.
“One piece of that would be to save fuel and reduce the power. The second piece would be to increase productivity. That sophisticated system will not be on the first machines, using what’s available today.
“As we’re doing that we’ll also learn about the power management, because that’s going to be really important. How we manage to bring down the power per metre that’s necessary will ultimately determine just how wide we can go.”
While the company expects initial interest will come from high-value crop producers, it hopes to expand its model range to appeal to broad-acre farmers with machines capable of much wider working widths.
Canadian producers interested in the initial model can contact the company about supplying one now, Henry says.
“In the first generation of this, we expect six metres is going to be our starting threshold in terms of working width. We do have ideas on how to stretch that out much more.
“If there’s a Canadian customer that has an application where 60 kW is the right one for what they want to get started with, we’ll put them in the hopper. At the moment we have estimates for what our pricing is going to be. We estimate this concept will be somewhere in the region of £200,000 (about C$346,000) for the six-metre version, and somewhere around £125,000 for the three-metre version.”