Got fusarium? Chances are North West Terminal in Unity, Sask., can use that wheat.
Next door to the terminal is a bioproducts plant, which is run by North West Terminal’s sister company, North West Bio-Energy. Since 2009, North West Bio-Energy has been producing ethanol. Today it also produces industrial-grade alcohol.
The distillation process can handle fusarium, said Jason Skinner, chief executive officer. Some of the DON (deoxynivalenol, or vomitoxin) is destroyed in the distillation process, he said, although they do have to blend down grain with DON. They also monitor the alcohol and dried distillers grain. The distillers grain is only sold into markets that can accept higher DON, he added.
Read Also
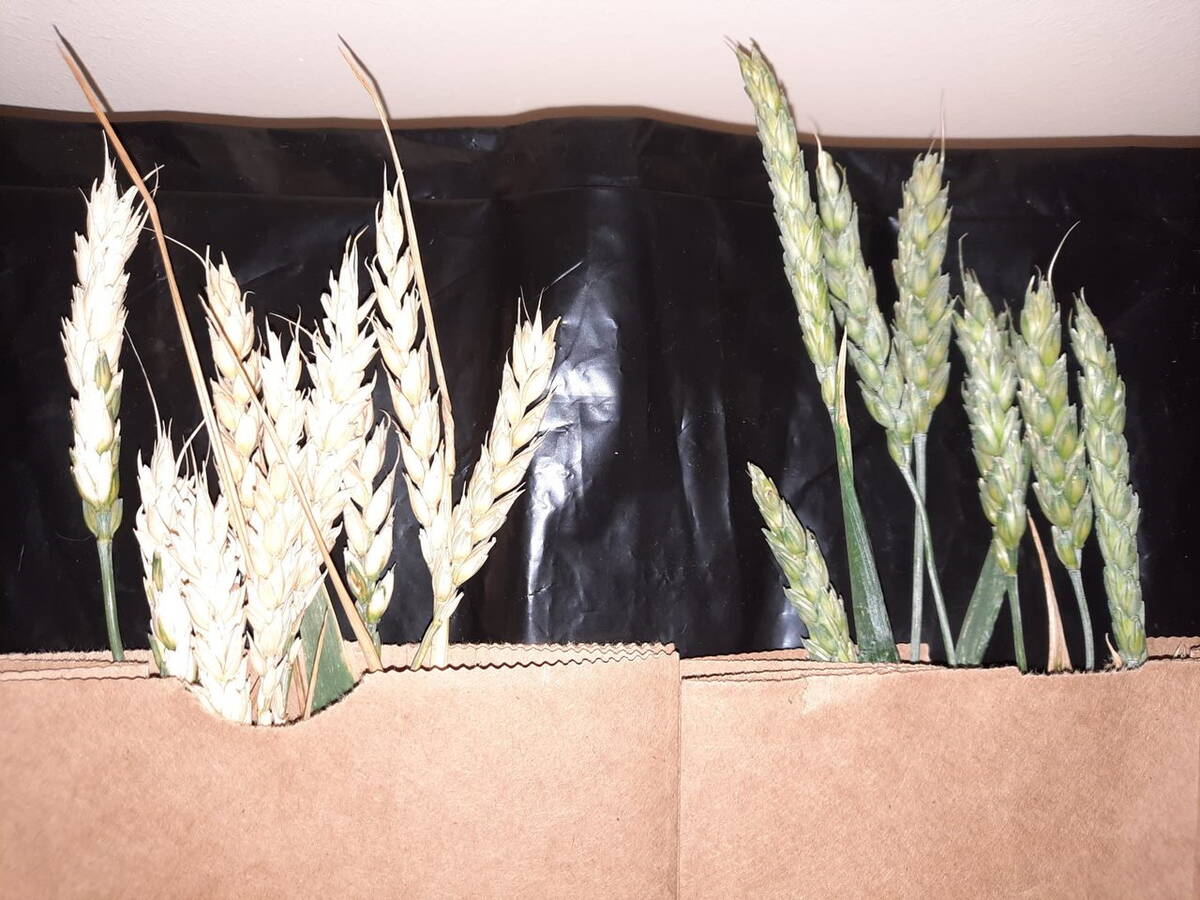
For wheat, aster yellows can be a disaster
If you or your agronomist detect aster yellows in a canola crop, you’ll be sure to find it also in an adjacent wheat crop, Ieuan Evans warns.
Higher-protein wheat does cause problems in the plant, said Skinner. “Wheats like durum or soft wheats or CPS wheats tend to work better in our process.”
Skinner took several farm reporters on a tour of the bioproducts facility. Reporters got an inside look at the facility, from the lab and control room to the distillation towers.
A biological process
Making alcohol is a biological process, involving living organisms such as yeast. In fact, staff feed the yeast urea and phosphate to boost performance.
Skinner compared it to feeding cattle. The difference, he said, is that their cattle are so small they have to be monitored differently. For example, spikes in lactic acid mean unwanted bacteria are consuming the starches, which will lower the alcohol content. The plant’s lab employees also test for things like alcohol and sugar content.
The first steps of alcohol production in a plant look a little like making beer. The grain starts out in the mashing tank. Water is added and heated. Employees then blast steam into the mixture to break down sugars and starches, and sterilize things. Eventually it becomes what beer makers call wort — sugars and solids. The sugars eventually become alcohol.
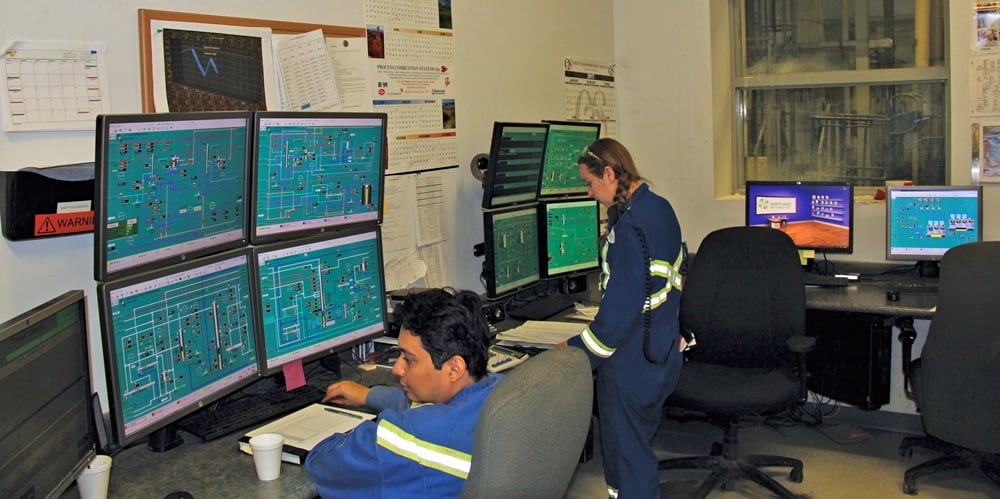
The wort is then transferred to one of four fermenters, where it sits for over 50 hours. Once a batch is done in the fermenters, North West Terminal has beer with about 10.3 per cent alcohol. However, instead of adding hops, employees distil the beer.
Cleanliness is also key. That means, for example, running caustic cleaner through the fermenters after each batch.
The beer moves to a beer well. That beer well supplies the distillation plant. From there, the beer is dropped into the first distillation tower, called the beer stripper. Skinner said that tower takes alcohol off the top of the mixture at a concentration of about 60 per cent. The stuff at the bottom of the tower is pumped to a different part of the plant and turned into dried distillers grain.
Meanwhile, the alcohol flows to the rectifying tower. Steam in the rectifying tower evaporates the alcohol, taking it to a concentration of about 95 per cent.
If the alcohol is destined for the industrial market, it’s redistilled several times to remove any impurities. It can then be used for potable alcohol in fortified wines, or in industrial applications. For example, food plants can use it as a sterilizer.
“Alcohol fits that bill because it is a food-grade product and they can use them in a lot of different processes where you may not be able to use a chemical-type sanitizer,” said Skinner.
Fuel-grade alcohol is ultimately sent to one of Saskatchewan’s blending stations — Suncor in Saskatoon or Co-op in Regina.
The business
North West Terminal is a corporation with about 1,000 shareholders, most of which are farmers from the region. The terminal has been in operation since August 1996. Since opening, the facility has doubled its storage capacity, expanded its rail car siding, and bought a share in Alliance grain terminal in Vancouver. About six years ago it hooked up to Canadian Pacific’s track, giving it access to both major railways.
And in 2007, the terminal decided to get into the ethanol business. Skinner said there were government incentives to get into ethanol at that time, along with a North American movement to expand into alternative energies. North West Bio-Energy produced its first truckload of ethanol in September 2009.
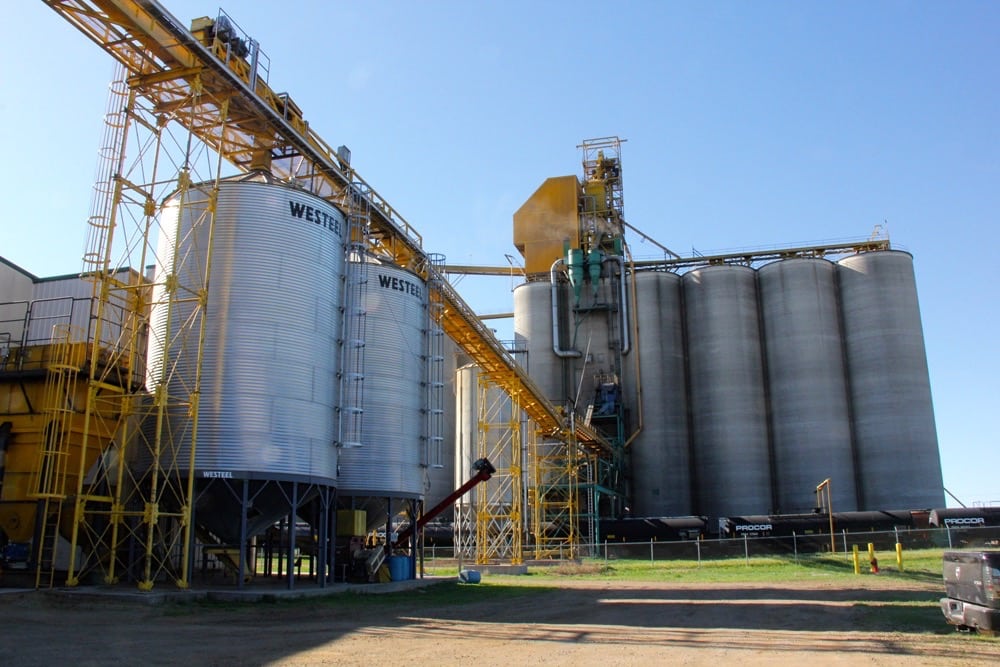
When it comes to biofuel plants, bigger isn’t always better.
“Profitability isn’t always a function of size in the case of ethanol plants. So there is room for smaller facilities,” said Skinner.
That’s because the price of ethanol isn’t necessarily linked to the price of inputs, Skinner said. Sometimes smaller facilities have an advantage because they’re buying grain from a shorter distance. That means fewer issues and less cost than sourcing grain from greater distances.
North West Bio-Energy moves alcohol into domestic, U.S., and global markets. Some sales are direct to customer, and some are through a broker. Skinner said that an industrial alcohol is “a commodity in the world market very similar to grain, so it trades in a lot of similar ways. One’s just liquid, one’s a solid.”
Industrial alcohol competes against alcohol produced from corn and sugar, exported from countries such as India and Brazil. As for the ethanol, the biggest competition is crude oil and gasoline, as ethanol is priced into the gasoline market.
“There’s a lot of competition out there in the world. We have to be efficient and able to compete with that.”
This article first appeared at AGCanada.com.