As Thomas Gress and a group of other baler product specialists at Krone stood in the shadow of an old Hungarian village church this past summer, they were surrounded by a group of journalists from several countries. Krone invited members of the media to a large farm on the outskirts of that village to see its new haying equipment in operation.
One of the machines the product specialists wanted to show was the BiG Pack 1290 HDP II large square baler, which offers the highest capacity and densest bales of any of the brand’s machines. According to Gress, the HDP II is the result of engineers designing a machine that pushes the limits of the previous line of High Densisty balers. It offers up to 70 per cent more throughput capacity than the 1290 HDP model. At the same time, it packs up to 10 per cent more material into a bale.
- Read more: Kubota expands its line and grows again
- Read more: New Vermeer bale wrapper
To get that capacity and density, Krone had to beef up the design of the HDP II version of the 1290.
“To get a higher throughput, we increased every component,” said Gress. “Starting with the pickup, a bigger cutting rotor and a bigger packer system, so we can put more material through the baler.”
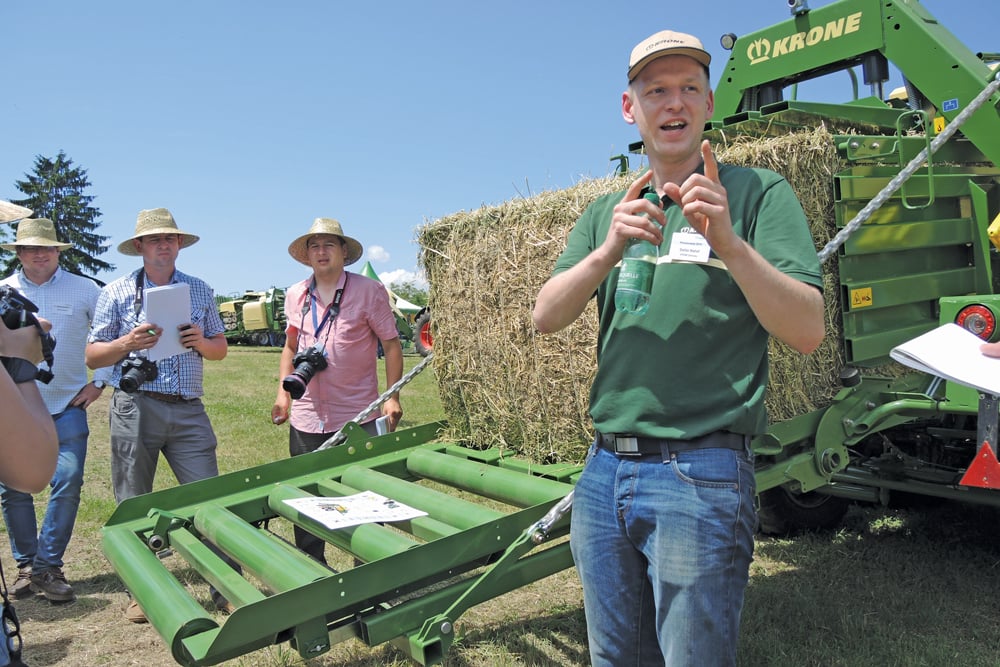
With so much density in the bales, the 1290 HDP II needs eight knotters to put two additional twines around the bales to keep them intact.
“When you have more material in the bale it wants to expand,” adds Gress. “That’s why we have eight Knotters on that baler instead of the six on the smaller HDP.”
The 1290 HDP II also has a massive twine storage capacity, capable of holding 27 bales of it. And the twine storage area lowers hydraulically to make reloading much easier.
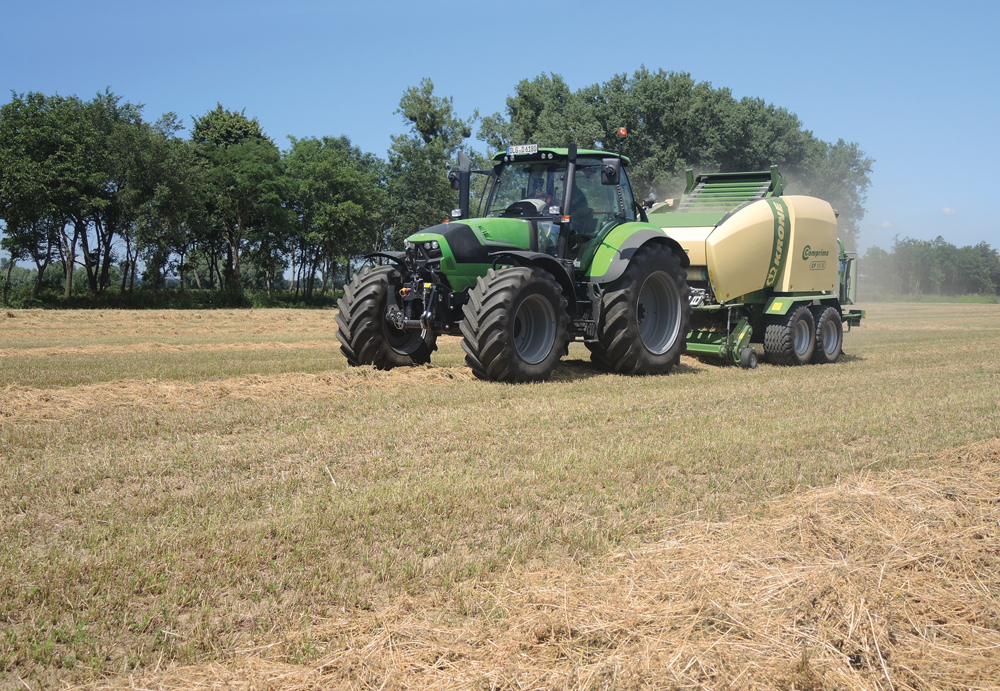
To make things easier on the tractor’s driveline, the HDP II uses a hydraulic motor system to start the flywheel, gearbox and plunger mechanism turning so there is less stress on the tractor PTO clutch when engaging it. Power flows through the baler in a newly designed, more direct, low maintenance driveline arrangement to reduce power loss. It also uses slip clutches rather than shear pins to protect system components.
“When you start, you activate the hydraulic motor from the tractor, which accelerates the baler up to 150 or 200 r.p.m., depending on the oil flow in the tractor,” he continues. “Then you activate the PTO shaft. So it’s not such a big challenge for the tractor to start the system up from zero. Then when you’re in motion, you can activate the pickup and cutter with a button.”
That also allows the pickup to be stopped independently of the rest of the baler functions in the event of a blockage.
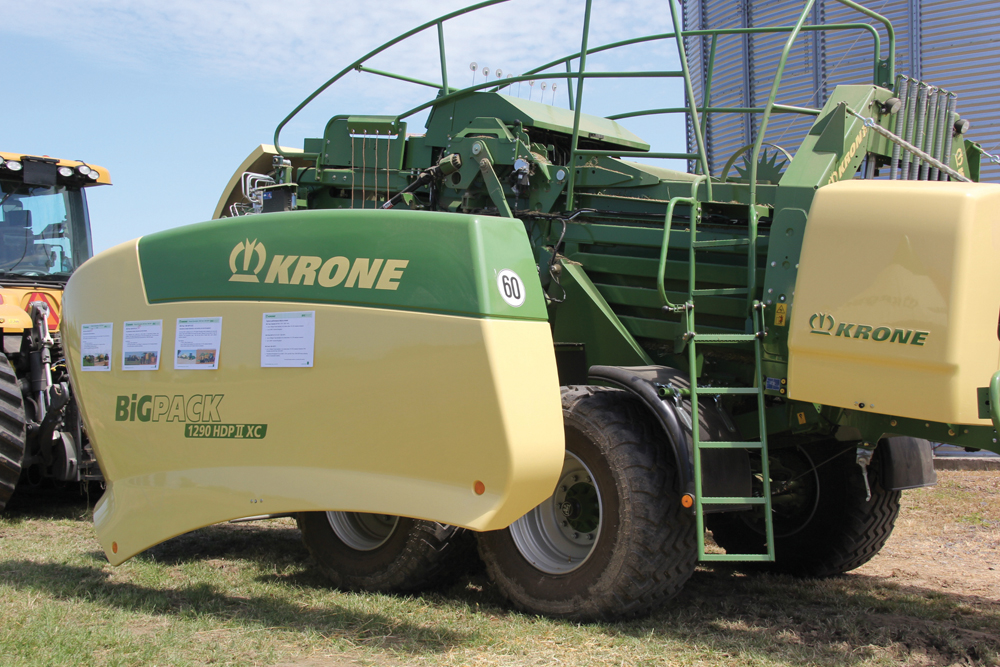
The HDP II gets a heavier flywheel, that weighs 600 kilograms. The larger mass provides more inertia and offers shock protection for the tractor. The number of plunger strokes per minute has been boosted to 45, and the faster-moving plunger forces material into a larger pickup pre-chamber.
The BiG Pack HDP balers can be outfitted with options that include an integrated moisture sensor in the bale chamber, an integrated weigh scale on the bale chute and a rear camera to help when backing up.
To help boost its competitiveness in the North American market, Krone has decided to relocate its head office and distribution centre from the Southeastern U.S. to Shelbyville, Indiana. The company is building an entirely new US$15 million facility that should be operational later in 2017.
“Krone wants to be the leader in balers,” added one of Gress’ team.
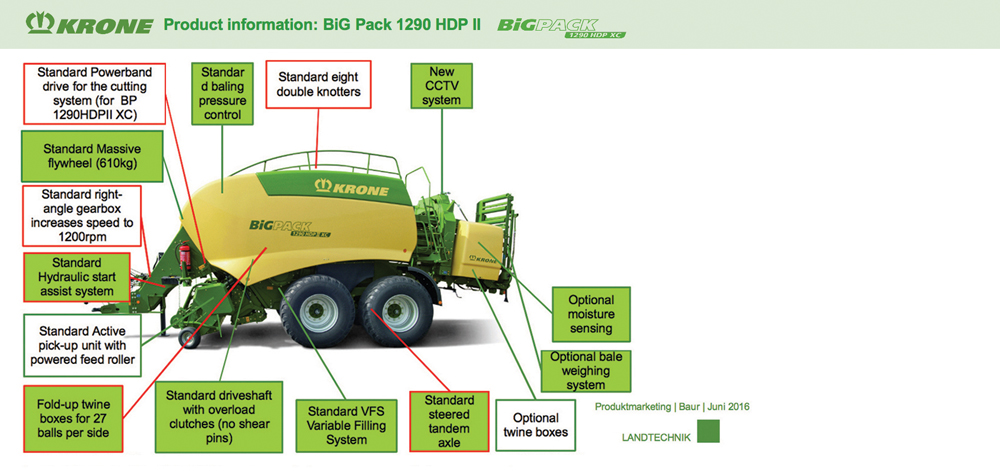