I can still hear it, the sound got louder and more prominent as we fought our way through the last days of the 2019 harvest season. One of the bearings on our straw chopper was nearing the end of its life, and luckily held together until the shards of the very last soybean stalk had been spat out the back of the combine.
The failing bearing wasn’t necessarily related to the wet harvest of last year, but it shows how our focus was strictly on getting the crop off, not on the mechanical soundness of our combine. If this was the case, how many other problems would be lurking inside the machine after we pushed it through the muck for weeks on end.
Why it matters: Farmers who check their combines for wear and tear caused by the mud harvest of 2019 will be field ready for 2020.
Recently, I spoke with Chris Plett, a combine mechanic based in Linden, Man., for CPC Ag Repair, to discuss some of the possible fail points and extra problems a combine might have after a wet harvest.
Plett was very quick to point out one of the most common areas of concern is the shoe augers. The beds and augers get coated with frost and mud, and it causes them to run rough.
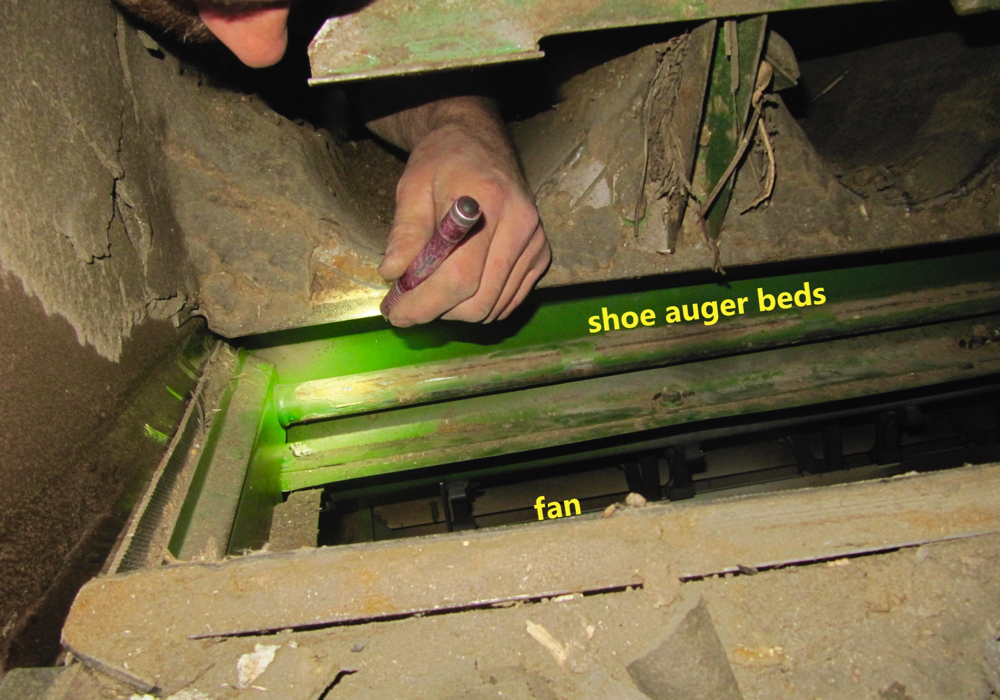
The shoe augers should be pulled out and inspected for damage, particularly where the bevelled gears attach to the auger shafts. The holes for the pin that connect these two parts may start to wear excessively and become oblong, creating more slop between the gear and the auger shaft.
The problem can be fixed by drilling out the hole to make it round again, and then adding the correct-sized bushing into the hole to ensure the original pin joins the two pieces securely. The other option is to change the entire auger altogether.
The shoe auger beds and surrounding areas should also be inspected for cracks in the metal. A particularly noteworthy area, at least on the 70 series John Deere combine we were looking at, is the region between the end of the shoe auger beds and the pre-cleaner.
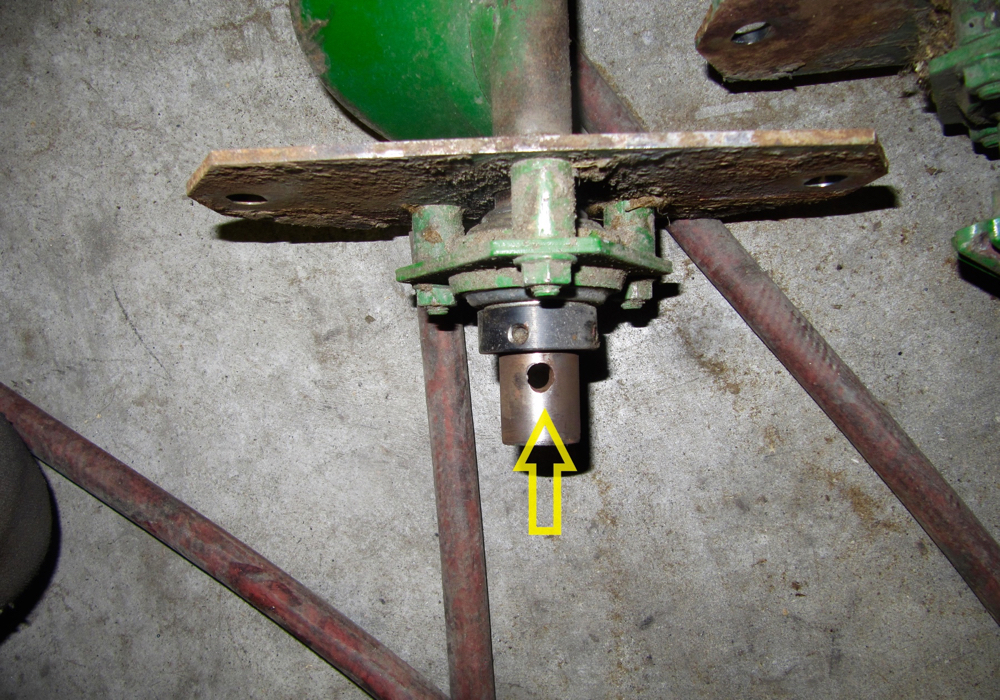
During a mud harvest, the seal on the front of the pre-cleaner will also become packed tight with wet material and frost. The excessive buildup almost extends the length of the pre-cleaner and it will ram into the metal that supports the shoe auger assembly. The extra stress on those support pieces will inevitably cause the support metal to become fatigued, and to crack and break. In extreme cases, those cracked pieces will fall directly into the fan and cause severe damage.
The pre-cleaner should be pulled back so this critical area can be inspected and repaired properly.
Check unloading components
It’s not only mud that causes issues; wet grain can lead to problems as well. A combine’s unloading system should be thoroughly inspected. Unloading crops like wet corn and wheat put large amounts of stress on the unloading components.
For example, the pulley on the countershaft that drives the unloader auger is a common wear point in the system and one that will deteriorate quicker in the harvesting of wet crops. The welds that hold the pulley together will crack and pulley failure will be the eventual result.
Plett also recommends checking the splines on the unloading system for excessive wear. The vertical auger is particularly susceptible to this type of damage as it will have a great amount of torque applied during the unloading of the combine.
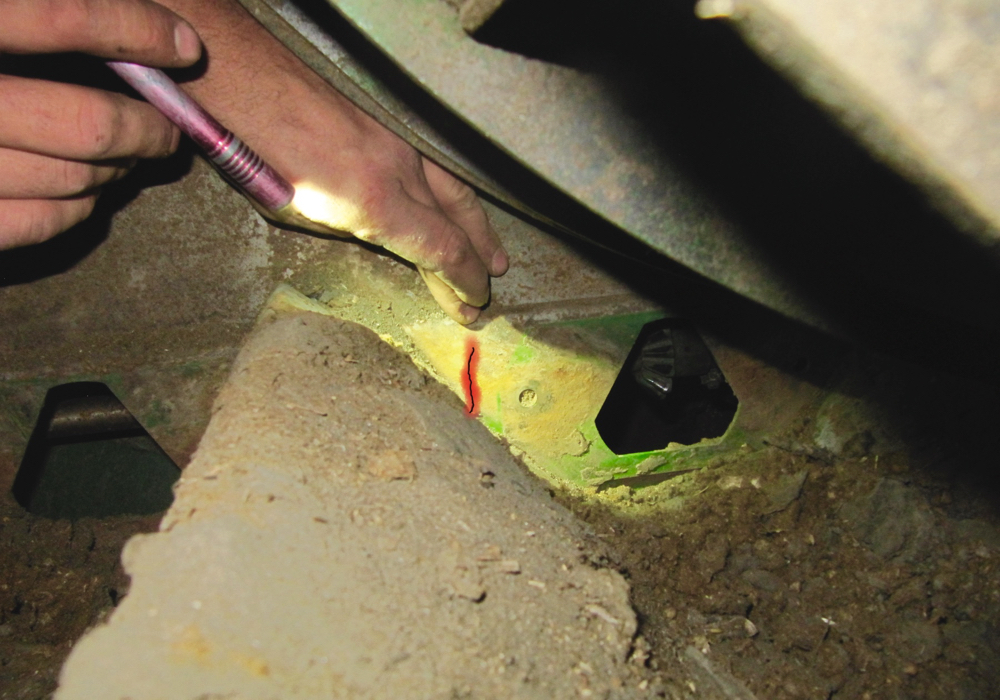
Change fluids
Not only do mechanical parts need to be taken care of after a wet harvest season, fluids are just as important.
“Hydraulic fluid will get way hotter running in the mud and hydrostatic (system) failure can be a direct result,” says Plett.
Changing fluid even before the recommended service interval might be necessary if the combine has spent the season running in extreme conditions. Hot hydraulic oil will lose its viscosity and begin to wear parts faster. When changing the oil, the system should be filled with a quality OEM oil meant to operate in the combine. Along with the fluid, the filters should be changed as well.
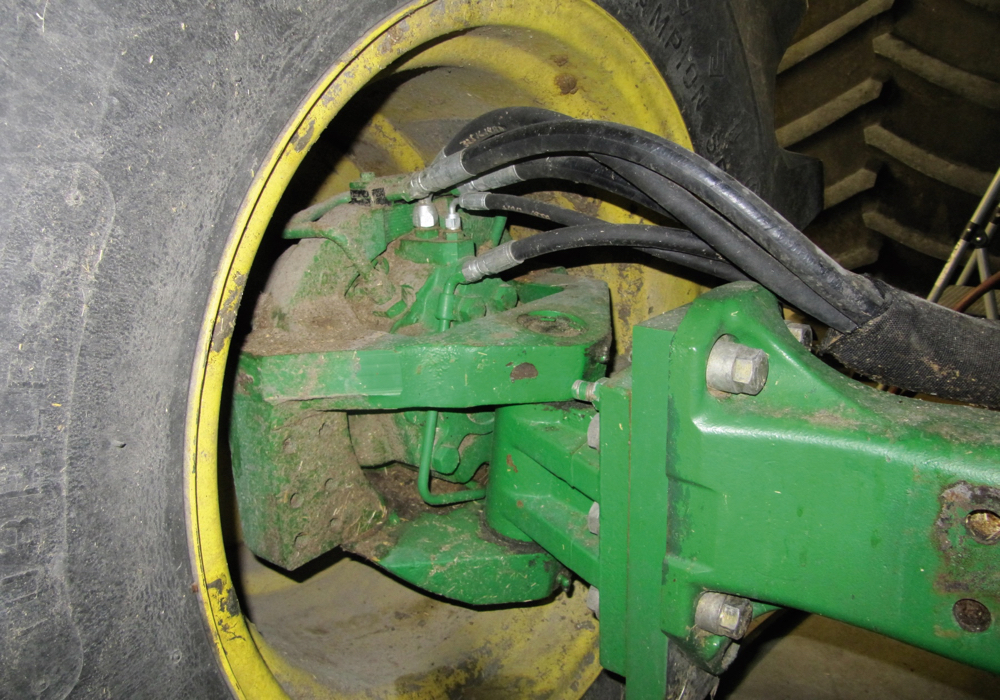
Plett wants to remind farmers the hydraulic oil in a combine is not like a tractor’s, which regularly gets discharged out and replaced when a hose is busted on an air seeder system.
Final drives on the combine will also be put under added stress during a wet year. The constant spinning and ploughing actions are harder on the gears inside. Aftermarket tracks will also stress final drive components. Changing the final drive gear oil is recommended after a mud harvest.
Looking toward future wet harvests, Plett suggests upgrading to a rear wheel assist system is a great option in the mud.
“The battle is against resistance. With a rear wheel assist you can have three motors helping the combine along — opposed to just one motor. This will reduce the load and strain on the combine’s drive system and help keep the combine’s hydraulic oil cooler,” says Plett.
He also pointed me toward a set of 1250/45-32 tires on the 70 series combine (9770 STS) we were looking at. He says he’s been happy with how the tires handled the mud this past harvest on his family farm and he will continue to use similar tires or tire upgrades to improve wet weather performance.
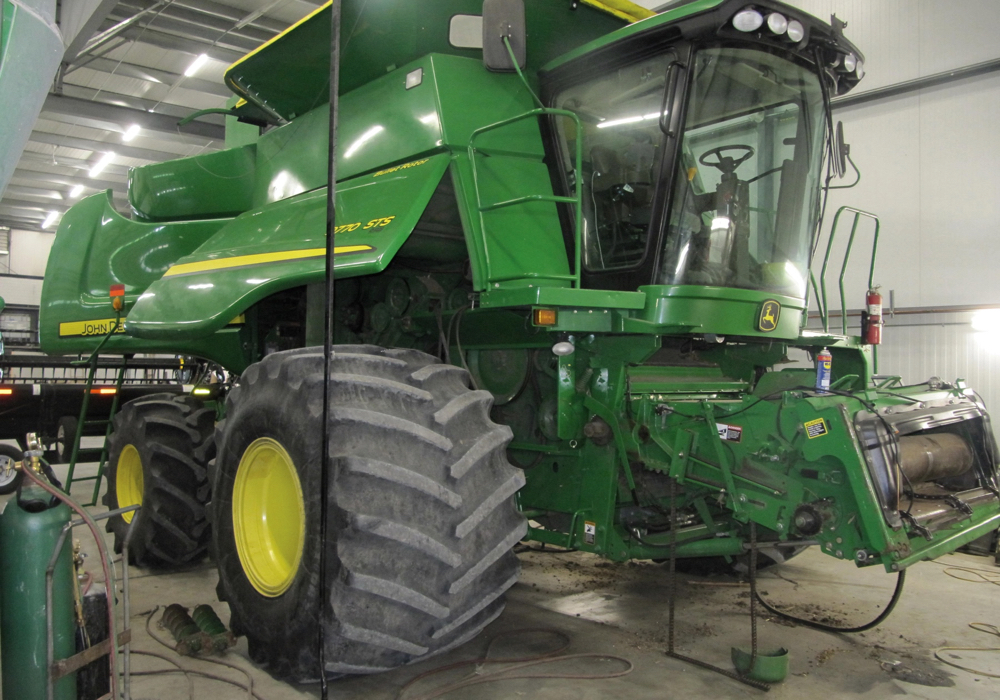