The horrific traffic collision that involved the Humboldt Broncos hockey team this spring has, among other things, sparked a debate around the safe operation of heavy trucks and the training of drivers. The truck involved in that incident belonged to a commercial carrier, not a farm. But across the Prairie provinces farmers enjoy some major exemptions from licencing and vehicle inspections for their heavy trucks. There is even less pressure on farmers to be trained in special driving skills and have their trucks comply with vehicle safety standards than on commercial carriers.
Read Also

Case IH, New Holland dealers to see more integration
CNH plans for “more than 15 new tractor launches, 10 combine launches, 19 crop production launches and over 30 precision technology releases between now and the end of 2027.”
What if that had been a farm truck? How long would it take politicians to abolish those exemptions in order to be seen to be doing something to prevent an incident like that from happening again? It was, after all, reaction to a roadway incident that led to the Lighting of Agricultural Implements Regulations that were instituted a little more than a decade ago.
Although farmers and their employees can generally operate air brake-equipped Class 3 (tandem axle) trucks without the endorsements on their driver’s licences that commercial drivers need, how many have been properly trained in air brake operation, pre-trip inspections and driving techniques? There is a lot of knowledge required to be highly proficient.
Here’s a look at some things drivers should know.
Air brakes
Air brake maintenance is key among safety requirements for all heavy trucks, and there are several key elements to consider in daily inspections — yes, daily inspections. First, the law mandates the speed at which a truck’s compressor must build up air pressure. It must not take longer than three minutes to build between 50 and 90 p.s.i. And the entire air system must be tight enough to limit air loss. At full system pressure, a foot pedal application held for one minute cannot allow more than three p.s.i. of air loss on a single-unit truck or four p.s.i. on a combination unit (semi).
Does your truck have manual or automatic slack adjusters? Did you know there is a process drivers must go through to ensure both types are properly adjusted?
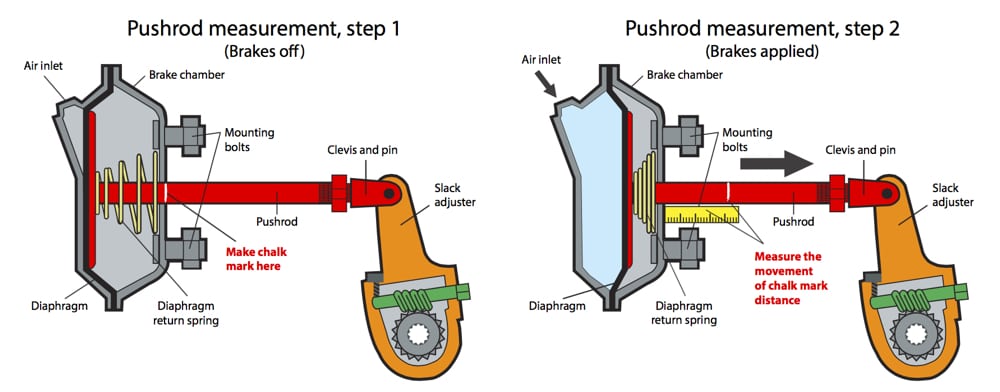
Slack adjusters do exactly what their name implies: they take the slack out of the brake mechanism, ensuring the brakes are properly adjusted. Older trucks (more than 20 years old) will most commonly have manual slack adjusters. A driver needs to crawl under the truck to manually set them.
There is a nut protected by a moveable collar on each manual slack adjuster. Using a 9/16 wrench, the nut is turned until the brake shoes touch the drums, and then backed off ¼ to ½ turn. If while turning the nut, the push rod and slack adjuster are moving away from the brake chamber, that’s a clear indication it’s being adjusted the wrong way. Be careful here, a young, inexperienced commercial driver made that error and mistakenly backed all his brakes off at a mountain brake check stop in B.C. many years ago. That caused him to lose all brakes on his truck on the downhill grade, which resulted in a major collision causing multiple deaths.
That incident was in part the impetus for provinces, such as Manitoba, to then create a special “S” air brake endorsement category that required drivers prove they knew how to properly set manual slack adjusters. So you can see how major events affect drivers’ and owners’ entitlements and obligations when it comes to heavy vehicles. The Humboldt incident might yet have some affect on farm truck regulations.
The law in most jurisdictions requires that the amount of pushrod travel allowed by slack adjusters be checked on a daily basis when the truck is used.
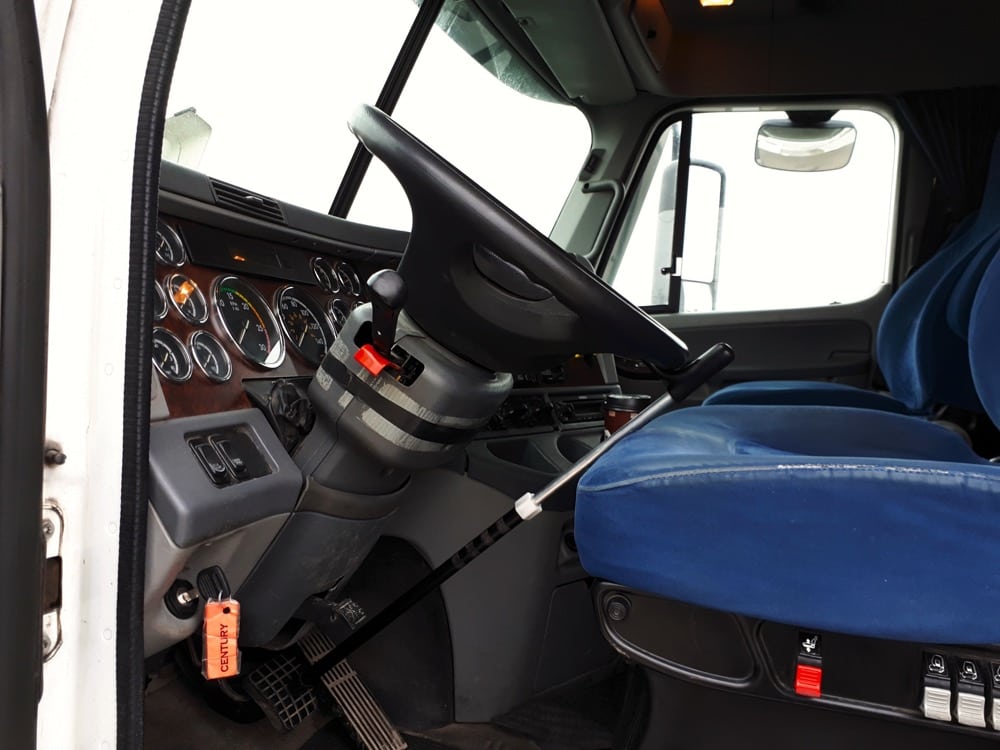
Automatic slack adjusters also need attention from drivers to ensure they properly self adjust. At the start of each day, a driver needs to make six full brake applications and hold the pedal down for a second or so each time. All of these applications need to be made with no less than 90 p.s.i. of pressure in the system. That allows the automatic slack adjusters to properly set their positions.
Once a driver confirms the system is building air properly, can hold it and either manual or automatic slack adjusters have been set up properly, the brake chamber pushrod travel should then be checked to ensure it’s correct.
With the wheels of the truck safely blocked to keep the truck from moving and the parking brake released, a mark should be made on the pushrod of each brake chamber. Then with the brake pedal depressed (either by a helper or with a “brake buddy” device) the amount of pushrod travel should be measured to ensure it’s within the allowable limit for the type of brake chamber the truck is equipped with.
Slack adjusters should be set so there is no more than ¼ inch difference in pushrod travel between brake chambers on the same axle. Uneven brake application pressure can not only cause unstable braking characteristics, but it can cause excessive heat buildup in a drum — and resulting brake fade — on one set of duals. That excess heat can also cause premature component failure.
Pre-trip inspections
At the start of their shift each day, commercial drivers need to do a pre-trip inspection of their truck (and trailer on a semi) and record the results. The CVSA (Commercial Vehicle Safety Alliance) sets out which components need to be looked at.
The inspection begins with checking the lights, then going under the hood and looking at critical engine and air system components. Next a look at chassis components including the frame, axle suspension and air brake components as well as the tires and rims.
Moving down the side of the vehicle, an overall look for damage is followed by a check of the fuel tanks, the batteries and then the air tanks. Most trucks have a “wet” air tank, which is where most of the moisture from condensation in the air system collects. Next are the primary and (usually) secondary air tanks. All three (if there is a secondary tank) should be drained at the end of each day, starting with the wet tank, then primary and lastly the secondary.
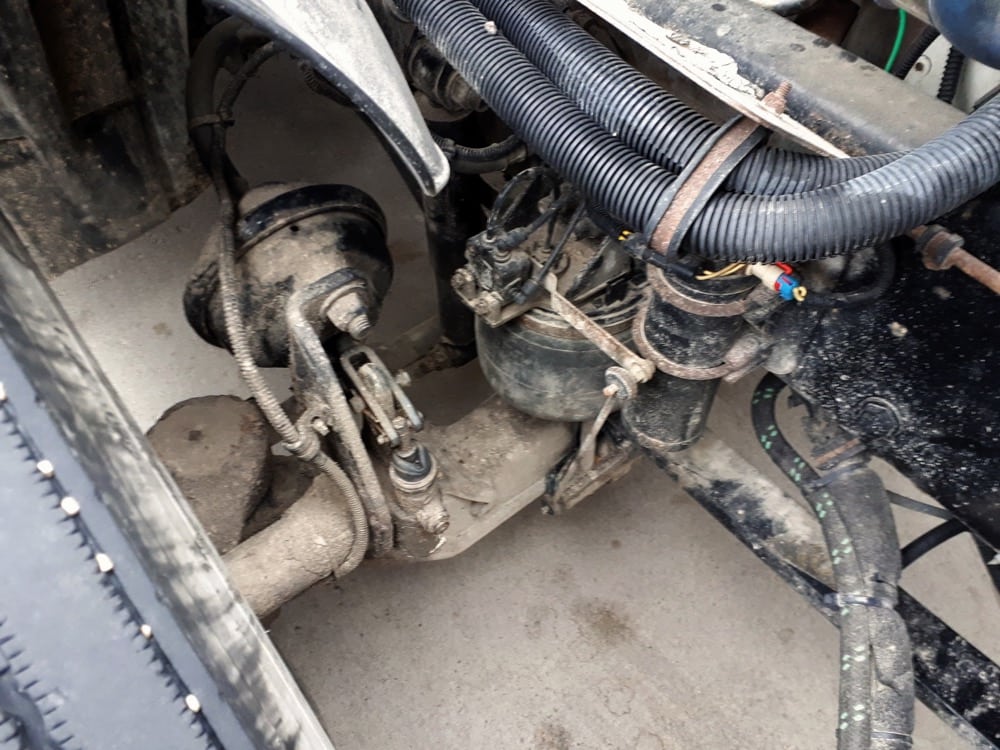
Even if farmers don’t need to record pre-trip inspections or take some trucks for periodic safety inspections as commercial operators do, their trucks need to be in good condition just the same. Like commercial drivers, farmers ought to consider getting into the habit of performing a good pre-trip inspection before hitting public roads.
If the police or provincial transport compliance officers stop a farm truck on the roadside for a safety inspection, it will be held to the same mechanical standard despite the lack of requirement for periodic safeties or documented pre-trip inspections. That means a farmer could end up with a ticket — or tickets — for all mechanical and safety defects found.
Why check the brakes?
No farmer will be surprised to hear it’s harder to stop a heavily loaded truck than an empty one. But just how much harder is it? This time it isn’t government regulations setting the rules, it’s the laws of physics that apply.
If the weight of a truck is doubled, it takes twice as much energy to stop it in the same distance. If the speed of a truck is doubled, it takes four times as much energy to stop it in the same distance. But if both the weight and the speed are doubled, it now takes eight times as much energy to do the job.
So drivers need to allow for much longer stopping distances when heavily loaded. And if the truck brakes are poorly adjusted and not preforming to their potential, the stopping distances can be greatly increased beyond those distances.
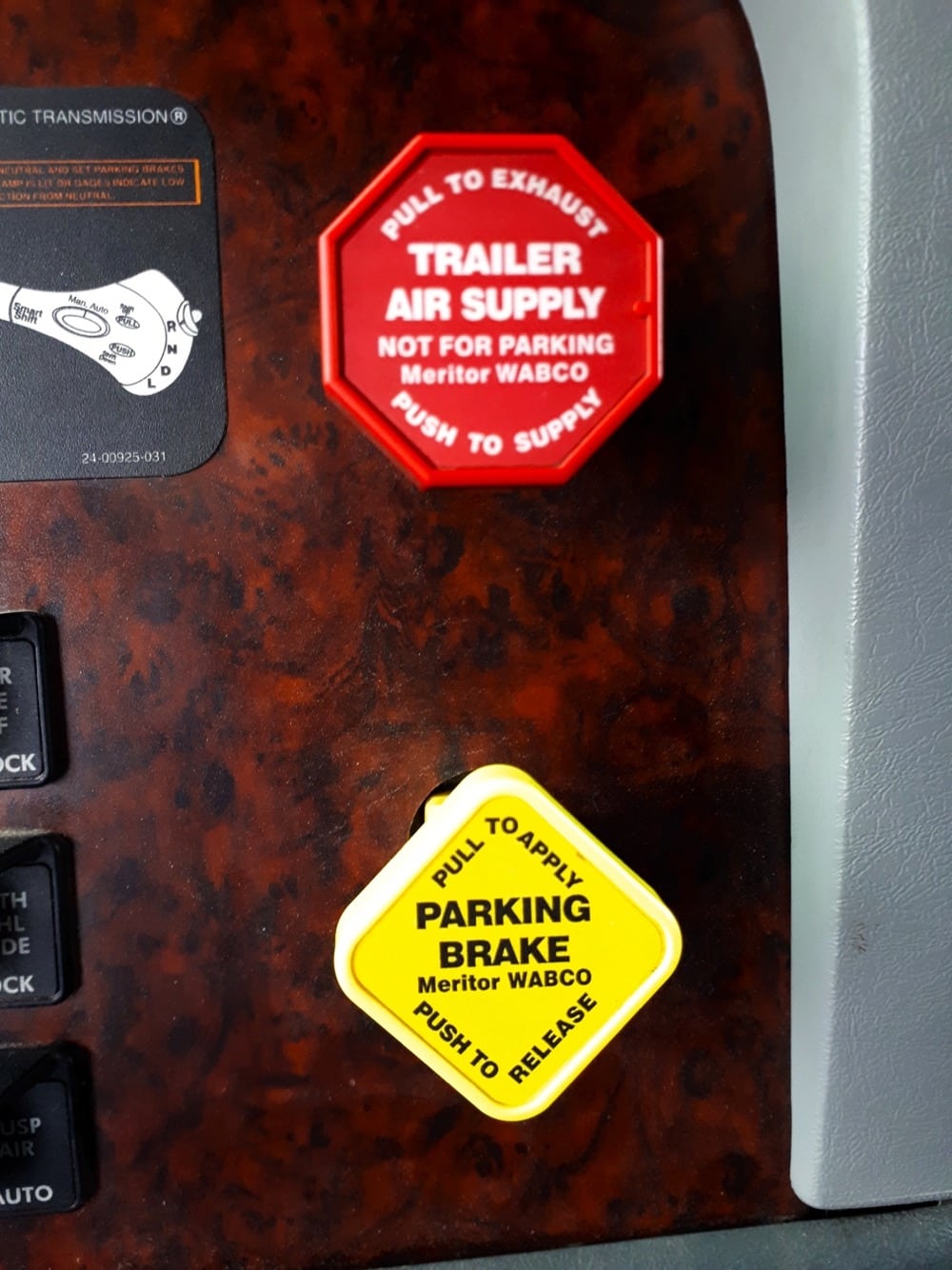