In July, farm editors traveled to Jackson, Minnesota to get a look at the newest Agco products bound for dealers’ lots.
With another 30,000 square feet just added to the plant, the manufacturing process has been subjected to yet another improvement on the assembly line. Among them are the addition of a lot more automated processes, including robotic laser cutters that ensure extreme precision when cutting out parts. Those parts now see much more robotic welding than ever before. Again, to ensure precision and accuracy. The robots also measure the fit up of component sections to ensure they are within tolerances before even beginning to fuse them together.
Read Also

Case IH, New Holland dealers to see more integration
CNH plans for “more than 15 new tractor launches, 10 combine launches, 19 crop production launches and over 30 precision technology releases between now and the end of 2027.”
But what AGCO management most wanted us to see was the all-new test and dyno facility designed to check the finished quality of new tractors before they are loaded onto a flatbed truck for delivery.
“There are two separate test stations,” says Arun Shankaran, the senior manufacturing engineer in charge of testing. “The first is the ‘Jounce’ test which can rock the tractor back and forth to simulate different track conditions. The purpose of this test is to make sure all the hydraulic and electrical connections are not loose and the tractor can handle anything in the field. We also have a PTO test. The purpose of that is to make sure the horsepower and torque specifications of the tractor are met through the entire RPM range.”
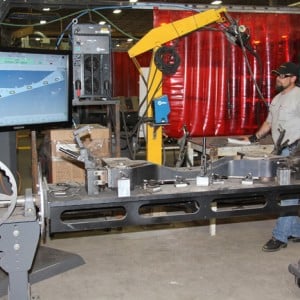
The jounce test has four separate stages as the tractor is shaken at various rates. If there are loose connections, they’re bound to show up after the tractor goes through this process.
“The next stage is the chassis dyno,” explains Shankaran. “We do a lot of tests on the dyno, high-speed test, steering test, braking test and so on. The whole purpose of this is to ensure a very high quality product goes out the door.”
Prior to building the dyno station, these tests were performed on an oval test track outside the factory. And while the tractors will still see a few laps on the track, the new procedure helps bump up the accuracy of that final evaluation.
“This (dyno station) is in addition to the road test,” adds Shankaran. “Some of the tests we couldn’t do before, like the jounce test. We had rumble strips, but now we have a more repeatable test. Now we have a more consistent and quantitative measurement for everything.”
For a video look at tractor testing at AGCO’s Jackson plant, click here.