A recent study conducted by Agriculture and Agri-Food Canada provides a glimpse into why some Canadian producers are using harvest weed seed control, the effectiveness of the technology and some of the challenges associated with it.
The 49-question online survey was conducted between the spring and fall of 2023. A total of 10 producers from Alberta and Saskatchewan who were early adopters of the technology responded to the survey. The results of the study were published in the September 2024 edition of the Canadian Journal of Plant Science.
While there have been various Canadian studies on impact mills, this is the first one to look at harvest weed seed control (HWSC) that incorporates actual on-farm experiences.
Read Also

Case IH, New Holland dealers to see more integration
CNH plans for “more than 15 new tractor launches, 10 combine launches, 19 crop production launches and over 30 precision technology releases between now and the end of 2027.”
AAFC research scientist Breanne Tidemann says even though researchers had previously conducted small-plot research and field trials on HWSC technology, there were some knowledge gaps and it was important to gather real world data about its use.
“No matter how much small-plot research or even field trial-scale research you do, it’s not the same as a farmer using it on all their acres for multiple years,” says Tidemann, who led the research study.
“They just get insights and experiences that we can’t get.”
Tidemann says while the survey used a relatively small sample size, the 18 weed seed mills that were part of it represented 60 per cent of the machines estimated to be in used in Canada in 2023.
Those results, she adds, will provide a baseline that researchers will be able to revisit down the road to determine changes to the adoption rate and who is using the technology.
The study focused on several key issues including who is using HWSC technology and why; challenges they have encountered with it; crops it is being used with; maintenance and fuel costs; and how effective it is in controlling problem weeds.
The survey results indicate most of the responding producers who use the physical impact mills for HWSC operate larger farms (10,000 acres or larger). Those producers equipped a majority of their combines (75 per cent) with the mills, but acknowledged they were strategic about their use since they had a limited number of the machines available.
Survey respondents indicated wild oat (60 per cent) and kochia (50 per cent) were the top weeds that motivated them to adopt impact mills on their farm.
Tidemann says she was somewhat surprised to see wild oat ranked so high.
“All the research that we’ve done has shown wild oat loses its (weed) seeds early so there’s some challenges using harvest weed seed control for wild oat. But I’m not surprised that it’s pushing people to try alternatives,” she adds.
The survey results also indicated operating a weed seed mill behind a combine adds an additional $1.40 in fuel costs per acre. Tidemann says it’s up to individual farmers to determine how affordable that is, since it largely depends on the size of the farms they operate.
On average, producers said it cost them about $1,500 a year in maintenance per impact mill, including greasing the mill as well as changing parts such as bearings and belts. Tidemann says it was difficult to pinpoint a precise figure since many respondents had only recently adopted the technology and were estimating what their costs would be. Longer-use adopters who completed the survey indicated annual maintenance costs of about $1,750 for each unit.
Participating producers were also asked about limitations or challenges they experienced when using the mills on their farm. Most respondents (70 per cent) identified mill plugging due to green material as a significant limitation they encountered. One of the primary sources of green material identified in the survey was kochia.
“A very large patch of kochia that’s essentially choked out all the crop, if you try and take that in one fell swoop, you will be unplugging the back of your combine. There’s got to be enough dry materials to push it through,” Tidemann says.
Despite that, a number of respondents identified kochia as the weed that showed the greatest response in terms of mill use. They also noted reduced use of herbicides with grassy weeds such as wild oats and green foxtail when using an impact mill. Wheat (90 per cent), canola (80 per cent) and lentils (80 per cent) were identified as the crops in which mills were most utilized.
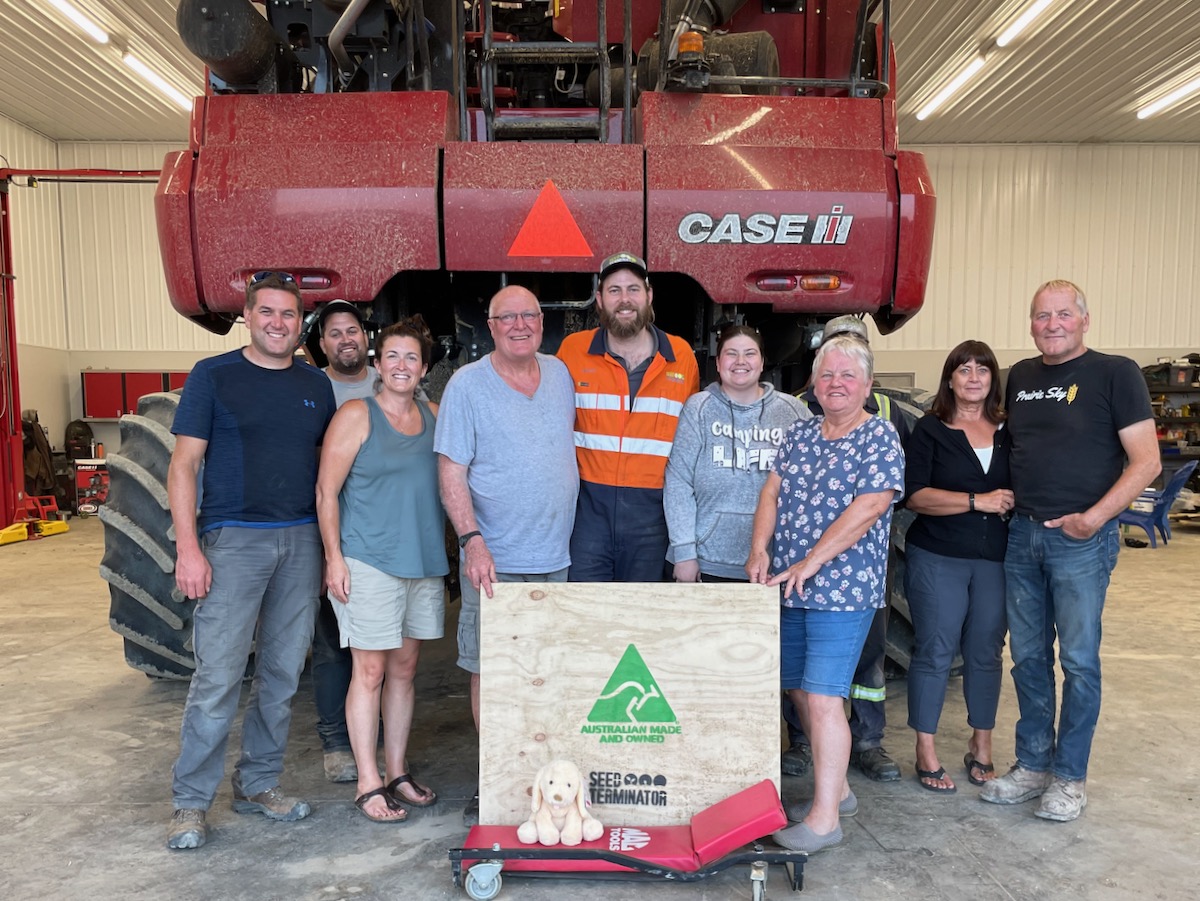
Producers were also asked to estimate how long it will take to recoup the investment they made when they purchased an impact mill. The most common response was three to five years (60 per cent) followed by six to eight years (20 per cent).
“It’s reassuring that those people that are adopting are going in with the mindset that it’s going to take some time and they’re not expecting an immediate response which is going to lead to people stepping out of it before they would maybe see the impact,” Tidemann says.
Respondents were asked to identify sources of information they consulted when considering the use of impact mills on their farm. The two most common responses were manufacturers/retailers and other early-adopting farmers.
“The mill companies makes sense,” says Tidemann. “The second one, early adopting farmers, was interesting. To me, what that’s saying is it’s all good and fine to have someone like me out talking to them, but you’re going to get a whole lot more bang for your buck if you have a farmer that’s actually using the thing. They want to hear from farmers who are using the machines.”
Resisting resistance
Jason Waldenberger was one of the farmers who participated in the AAFC study. He operates a 6,500-acre grain farm just north of Moose Jaw and has been using an Australian-manufactured Seed Terminator impact mill there for the past three harvests.
Waldenberger says he’s an “easy sell” when it comes adopting new technology and became interested in HWSC equipment several years ago after meeting a fellow farmer who was already using it. He was prompted to start using it himself after noting growing chemical resistance among weeds in the fields where he was growing pulse crops.
He says participating in the study was a no-brainer since anything producers can do to help the research community also helps themselves.
“We’ve got some fantastic people working in our industry,” he says. “I think anytime we can work with those kinds of people or pass along information and vice versa, they can then do really good, steady work and help us make better decisions and give us feedback on what they’re finding.”
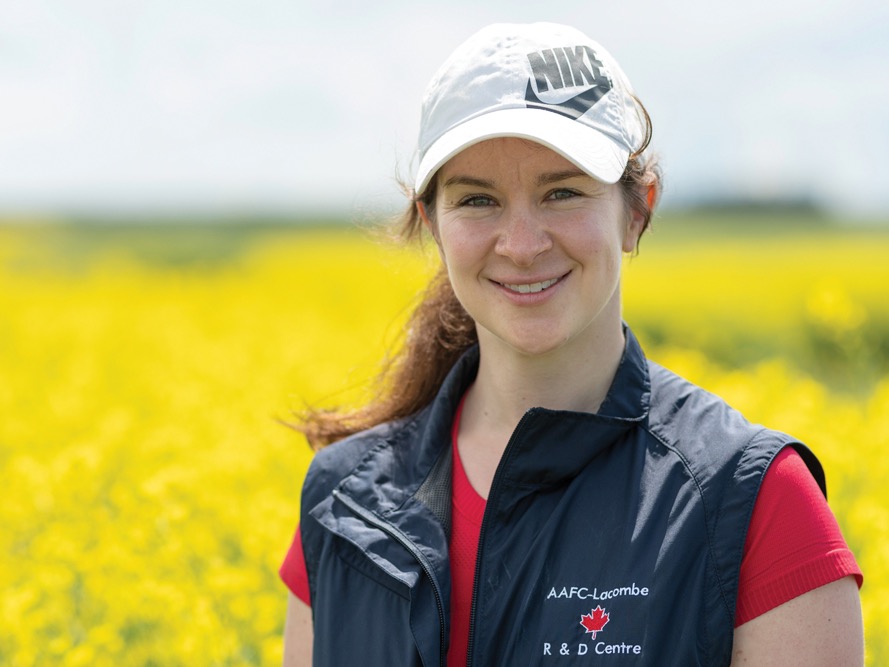
Tidemann says the data gathered through the survey could help manufacturers make adjustments to their products to address some of the concerns producers raise.
It may also help provide some direction for future research in terms of HWSC technology. Survey respondents were asked to identify research that was still needed regarding impact mills. The three most common responses were efficacy on weed densities, their impact on precision spraying and grain loss calculations.
“There’s still lots of things that we don’t know (about the technology) and this gives us an idea of what’s important on-farm,” says Tidemann.
HOW IT WORKS: Appendage for destruction
You may know what a weed seed mill is, but you may not know how it works.
Here’s a snapshot of what it does and how it helps prevent weeds from growing and spreading.
First, the mill is attached to the rear of a combine. Then as a crop is harvested, weed seeds come out of the back of the combine and are fed into the mill where they are spun at a high rate of speed which damages the weed seeds and renders them nonviable. This material is then spread back in the field.
In addition to controlling weed seeds, the mills also help stop the spread of weed seeds during harvest, lower herbicide costs, and reduce selection pressure for herbicide resistance.
Some of the most popular HWSC devices include the Redekop Seed Control Unit, the Integrated Harrington Seed Destruction, the Seed Terminator and the WeedHOG.