Ethanol, biodiesel, cellulosic, second generation, next generation — even the terms associated with biofuels are confusing, so it’s hardly surprising that a lot of people aren’t too clear about what biofuels are, what they can be made from, how they are made and how likely it is that biofuels are going to end up in their car’s fuel tank.
Biofuels are fuels derived from living plant material. Petroleum-based gasoline and diesel are fossil fuels derived from decomposed plants, marine algae and animals that died 300 million years ago and were gradually compressed underground into oil. Biofuels are produced from plants growing today.
Read Also
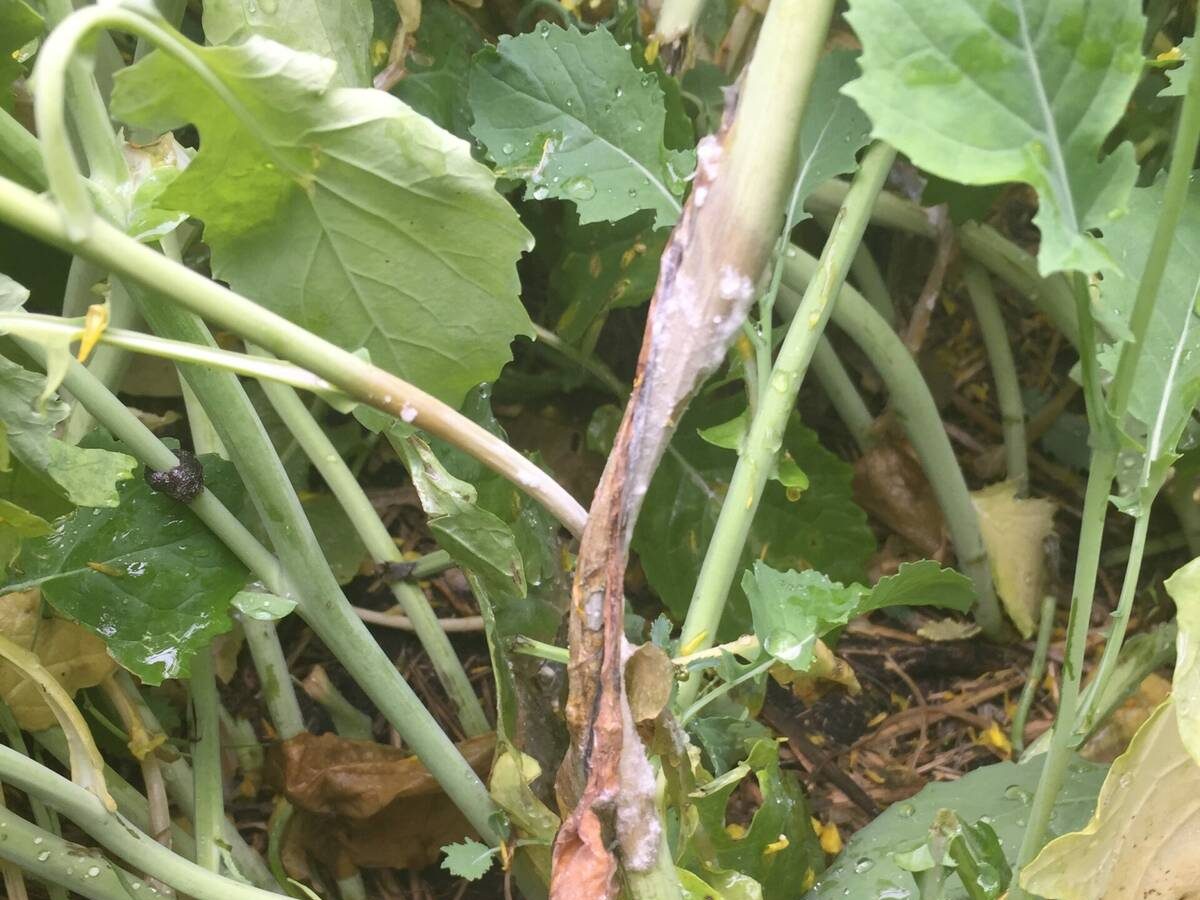
Good news, bad news for fungicides meant to fight stem rot in canola
A report shows overall insensitivity of sclerotinia to three fungicide groups hasn’t changed in a big way between 2010 and 2024 — but shows some sclerotinia populations have been discovered with elevated insensitivity to all three.
There are two general classifications of biofuels: biodiesel and bioethanol. These are also referred to as first generation biofuels.
Biodiesel
Biodiesel is generally made from oilseed crops like canola, rapeseed, soybeans and corn, but it can also be made from animal fats and used cooking oil from restaurants.
Biodiesel is a great alternative to petroleum fuels because it has lower greenhouse gas emissions, has lower particulate emissions, which improves air quality, and produces less sulphur oxide and nitrogen oxide emissions.
The problem with using biodiesel as a fuel in Canadian vehicles is that, just as vegetable oils become cloudy if you put them in the fridge, biodiesel begins to form crystals and solidify when the temperature drops below zero. Because of this, biodiesel in Canada is blended with petroleum at rates of only five or 10 per cent.
Bioethanol
Ethanol is made from alcohol produced through fermentation of starches and sugars in cereal crops such as corn and wheat. In the U.S. ethanol is generally made from corn, while in Canada and Europe it is made mostly from wheat or a wheat/corn blend.
One hundred per cent ethanol can be used as a direct substitute for gasoline in automobile engines. Brazil is the only country that offers both petroleum gasoline and ethanol at its pumps. Brazil switched to ethanol 40 years ago and is a world leader in re-designing existing vehicle combustion engines so that that they can use either 100 per cent ethanol or 100 per cent petroleum derived gasoline at any time.
Standard Canadian cars can’t operate on anywhere near 100 per cent ethanol, and car manufacturers are reluctant to make the investment in infrastructure that would be required for their cars to do so. Ethanol is limited to a five or 10 per cent mix in petroleum gasoline in North America, a level that will not cause damage to typical engines.
Second generation
The term “second generation biofuels” generally refers to cellulosic ethanol — ethanol made from fibrous plant biomass such as wheat or flax straw, corn stover or even cattails. Cellulose is one of the main constituents of woody material like stalks or after-harvest crop residue.
It’s fairly easy to extract the sugars from grains such as corn or wheat to convert them to alcohol and make traditional ethanol. Cellulosic ethanol is more difficult to make, because the plant biomass is much more difficult to break down.
Imagine cellulosic material as the cables in a suspension bridge. It’s made up of long fibres that are twisted around each other and bundled together to give incredible strength. Those fibres are held together with lignin, a natural polymer that forms a glue to bond them together. Cellulosic fibres are often used in construction because of this strength. Hemp fibre, for example has been used to reinforce concrete.
To break cellulosic material down to get the sugars out is complicated, energy intensive and costly. At least half of the cost of making ethanol from cellulose is the pre-treatment that is required to break up the lignin-cellulose material to release the sugars to produce alcohol.
Around the world many people are trying to figure out how to break down cellulosic material more efficiently and at a competitive cost. Currently there is only one commercial-sized cellulosic ethanol production plant, which was built in Crescentino, Italy in 2012. Another plant planned for Brazil could be operational this year.
From the Alberta Farmer Express website: In win for Big Oil, U.S. proposes biofuel mandate cut
Biofuel economics
Most biofuel production around the world relies heavily on government subsidies. The Canadian government has announced that its biofuels subsidy program will end in 2017. Although there is concern that investment in the Canadian biofuel industry may be hampered without subsidies, construction of some new facilities seems to be going forward. U.S. agri-food company Archer Daniels Midland, for example, is planning to build a 265-million-litre-per-year biodiesel plant in Lloydminster, Alberta, next to its existing canola crushing plant.
“The bioethanol companies that make ethanol in the U.S. and Canada based their business models on $3 per bushel corn or wheat. Once a bushel of corn is $6 to $10, the cost of buying that material is almost prohibitive for them to make money,” says Dr. David Levin, associate professor at the Department of Biosystems Engineering, University of Manitoba.
“Fuel is a commodity where you have to make a lot of it and it has to be low cost. If it costs more than petroleum, nobody will buy it because there is no incentive. That’s why there have been subsidies so companies can make it at a cost and be competitive with petroleum fuels.”
At the end of the day, the economic viability of any alternative fuel is a function of the cost of a barrel of oil. “When oil to make petroleum based fuels and other chemicals is $60 to $90 a barrel, the cellulosic biofuels are marginal, they can’t compete,” says Levin. “If a barrel of oil goes up to $120 or $150 a barrel as it did in 2008, then all bets are off and all of those alternative fuels become more attractive.” †
Angela Lovell is a freelance writer, editor and communications specialist living and working in Manitoba. Find her online at www.angelalovell.ca.