With modern technology comes modern problems. As more technology is integrated into seeding equipment, more devices require a power source — and in some operations, this may exceed the output of the 12-volt tractor system.
The technology in modern seeding equipment has changed from the days of the on/off and up/down switch of early drills. New equipment may call for monitors, touch screens, tablets and switch boxes all requiring power, on top of the cellular phone and conveyor remotes needing to be charged periodically as well. The abundance of devices requiring power can become too much for a tractor’s built-in system. Most tractors come with a single 12-volt outlet, when producers either need multiple power points or, if they’re already using a multi-plug, see these plugs generating undesirable heat.
The most common solution to this problem has been to add an inverter to the tractor cab. Most hardware stores will have a simple and relatively cheap (likely under $100) 200-watt inverter on the shelf. Teed off the battery of the tractor and routed into the cab, ensuring safe wire placement, the inverter unit should be kept out of the way but also easily accessible. This placement will be at the installer’s discretion.
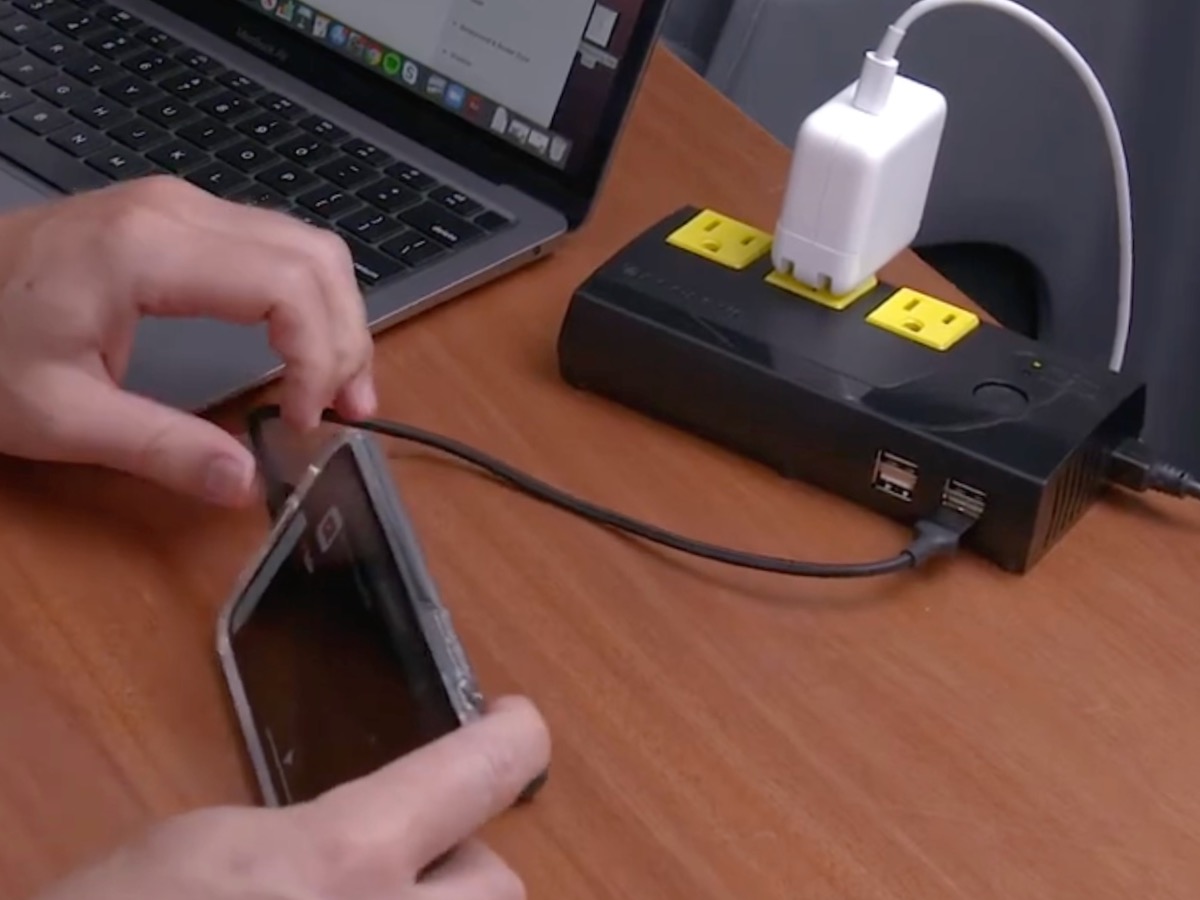
Many of these inverters will come with one or two AC and two to four USB ports, for more power distribution. Both outlet types will be important: USB A or C for charging devices, and AC ports to provide power to any standard two-prong plug. The charging ports will generally draw around 20 watts per device. While the primary function will be charging various devices, any monitors or control boxes normally routed to the tractor battery can also be connected to the inverter power input, potentially cutting down on the wiring length by half.
Read Also

Case IH, New Holland dealers to see more integration
CNH plans for “more than 15 new tractor launches, 10 combine launches, 19 crop production launches and over 30 precision technology releases between now and the end of 2027.”
Larger inverters, in the range of 1,000 to 3,000 watts, will come at a higher purchase price, up to $700. While excessive for charging electronics in the cab, they may come in handy in emergency repair situations. The ability to run a variety of power tools may save a trip back to the yard, and valuable time. Online retailers are abundant, so check reviews to make sure you’re buying a quality product. While the demand for this aftermarket install will be highest during seeding season, it may be best tackled in the off-season.
In general, this addition is meant to make the operator’s job easier and more efficient. Having sufficient power, avoiding juggling power cords, and reducing stress on the factory system are all benefits.
As with any DIY project, proper safety precautions should be followed to avoid damage to the equipment. Be sure to double-check with your local dealer, but this modification should have no effect on the manufacturer’s warranty.
As manufacturers come out with new models, it is assumed one of them will be the first to make this inverter a factory option — assuming they follow automotive manufacturers’ lead. As the need for power in the cab increases, these manufacturers will have to heed customers’ needs and make adjustments. Here’s hoping they include more than just a single outlet.